Recommended Products in this Industry
AESSEAL® have been providing sealing solutions to the food and beverage industry for many years and recognise the importance of providing solutions will not compromise the quality of the manufactured product.
All AESSEAL® products are supplied to this industry with FDA and EU Directive 1935/2004 compliant wetted materials as standard. Products are manufactured in accordance to Good Manufacturing Practice (GMP) assuring compliance to EC2023/2006 and are marked with the appropriate labelling, giving customers the confidence that AESSEAL® products are suitable for use in their applications.
AESSEAL® offer a range of seal support systems that can help to reduce water consumption, from FlowTrue™ that allows precise flow control on quench to drain systems to the EasyClean™ system where recirculating systems are acceptable. The split design of the EasyClean™ ensures the vessel can be thoroughly cleaned and inspected, minimising the risk of bacteria entering the process.
AESSEAL® have created a brochure specifically for the food and beverage industry making it easy to find the right sealing solution for a specific pump found in the industry.
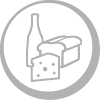
Get access to the industry brochures
Industry Solutions
Dairy
Food safety is of paramount importance in the dairy processing industry. Each product component in direct contact with the process must meet stringent hygiene standards.
AESSEAL® offers certified and approved products to meet global standards: such as FDA and WRAS certification as well as EHEDG standards.
Corn
The past several years have seen significant growth in the use of mechanical seals in the Food Processing industry. AESSEAL® products have been applied successfully to applications in each stage of the corn milling and refining process.
Wet Milling
There are several steps in this process. First, the incoming corn is inspected and cleaned, then steeped to begin breaking the starch and protein bonds. The next step is a coarse grind to separate the germ from the rest of the kernel. The remaining slurry; consisting of fibre, starch and protein, is finely ground and screened to separate the fibre from the starch and protein. The starch is separated from the remaining slurry in hydrocyclones. The starch can then be converted to syrup, or made into several other products through a fermentation process.
Refining
After the starch is cleaned and separated it can be sold in its raw state or it is further refined and converted to glucose syrup. Starch slurry is converted to glucose syrup and refined to different grades of sweetness. The refining of corn syrup is a complex process requiring maximum equipment reliability and enhanced productivity gains are possible through the selection of properly designed AESSEAL® components.
Sugar
Sugar factories have numerous pieces of rotating equipment requiring sealing. With the ever-increasing demands for improved efficiency, reduced waste and effluent and improved equipment reliability, there is now an industry shift from traditional sealing methods.
The use of modern high-quality cartridge mechanical seals and associated support systems is now becoming the industry norm. These seals guarantee plant uptime and significantly reduce water wastage and the resultant effluent.
Based on experience gained over the past 20 years in the sugar and syrup Industries, AESSEAL® has successfully sealed most applications in the modern sugar mill. When correctly installed and supported, companies can confidently expect up to three years without any maintenance.
Chocolate
Applications in the chocolate manufacturing process range from pumps to specialized processing equipment.
Each of these applications need a mechanical seal and system that works effectively to support the food safety requirements of the chocolate industry.
The industry is still using soft packed glands or OEM seals that do not, in many cases, give a reasonable life. AESSEAL® has installed mechanical seal technologies which improve pump life. The industry has embraced our modern double seals used in conjunction with seal barrier systems. This approach coupled with FDA compliant barrier fluids provide a significant improvement in reliability and a fast return on investment to our customers.
Brewing
Faced with high temperature environments and start-stop equipment practices, the brewing industry has many sealing challenges.
Product evaporation efficiency can be improved with the correct sealing system and effective fluid film control is important when sticky product hardens around the seal faces.
AESSEAL® has mechanical seal, support system and bearing protection technologies which increase reliability in all stages of the brewing process, including pumps start up:
Hot Worts Transfer
Kettle Pumps
Condensate Pumps
Cleaning in Process Pumps
Bottling Plant