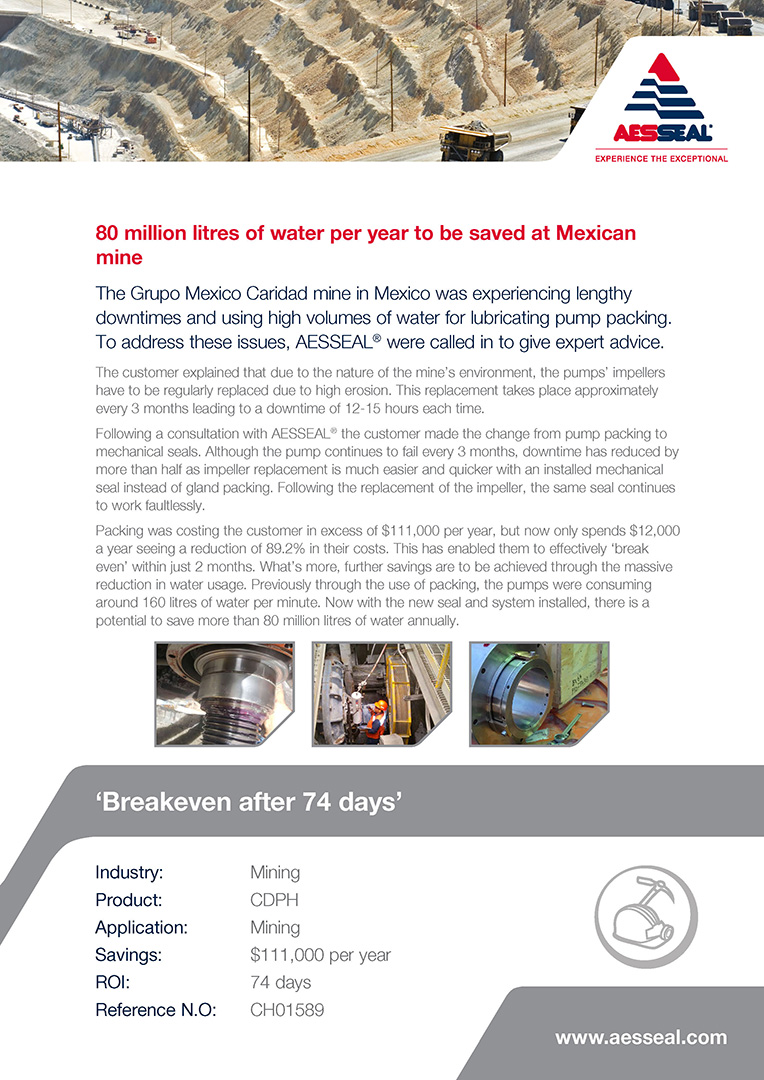
The Grupo Mexico Caridad mine in Mexico was experiencing lengthy downtimes and using high volumes of water for lubricating pump packing. To address these issues, AESSEAL® were called in to give expert advice.
More Industry Related Content
By Raúl Castro
How did AESSEAL® get involved with this company and what was the problem?
We made contact with the company through a distributor. They were having problems with their pumps because the mine is a tough environment which takes a heavy toll of the equipment. In this case, there was a lot of wear on the pump caused by the abrasive nature of the ball mill slurry. They were also using huge amounts of water in order to lubricate the gland packing.
Were these problems affecting production?
Yes. The excessive wear meant that the pumps’ impellers had to be replaced every few months. This took anything from 12 to 15 hours each time, which adds up to a lot of downtime over the course of a year.
How did you propose to solve the problem?
We recommended that they should replace the gland packing with an AESSEAL® double mechanical seal. The mine is located in a very dry area of the country, so one of the things which helped to convince them to change was when we told them that the mechanical seal would make a big difference in reducing the excessive water usage. We also explained that it would help to prevent the corrosion which was causing such a lot of damage to the equipment.
Did this make it easy to convince them to make a change?
Not really. It took almost three years before they were ready to follow our recommendations. Companies are sometimes reluctant to change even when the system they’re using is not working very well.
Did the new seals make a difference?
They worked exactly as we said they would, reducing water usage and minimizing the rate of corrosion. But the mine is such a difficult environment that they still had problems with the pump, and they were still having to replace the impellers every few months. The difference was that with the AESSEAL® mechanical seals, this took much less time, to the extent that it reduced the plant downtime by more than half. And even though they had to replace the impellers, they found that our seals were still in good condition, so the same ones could continue to be used for more than a year before they had to be replaced.
Are they still working well?
Well, the original order was for 12 seals, of which a few are still in place. We thought that we could improve their performance still further with the use of super duplex or Alloy255, but unfortunately there was a change of management at the mine, and they finally decided that they were going to revert to gland packing.
Is there a chance of any further business with this company?
We believe so. Going back to gland packing means that they’re still trying to deal with the problems of excessive water usage and a lot of downtime. But we’re still talking to them, and we’re optimistic that we can do business with them again by convincing them to go back to using an AESSEAL® product, and to invest in an upgrade which would save them a lot of money in the long term.