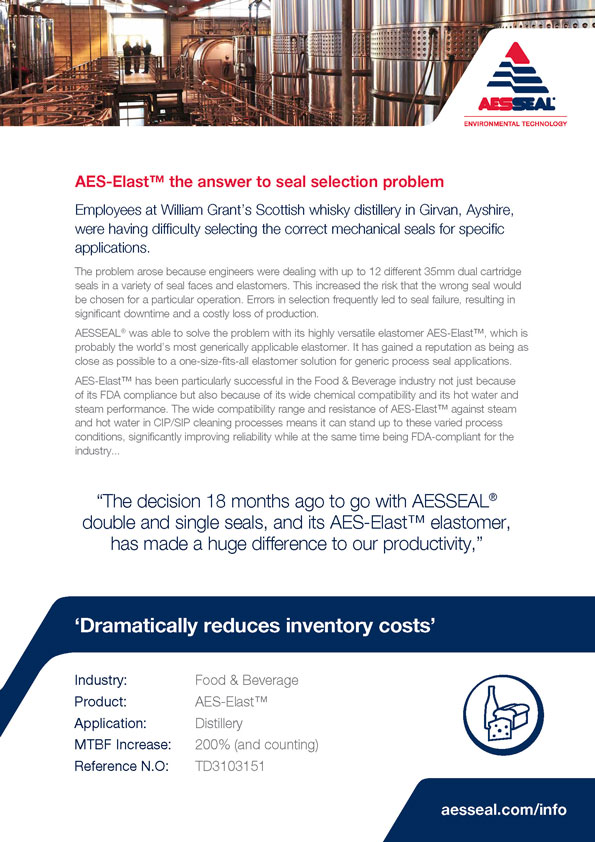
Employees at William Grant’s Scottish whisky distillery in Girvan, Ayshire, were having difficulty selecting the correct mechanical seals for specific applications.
More Industry Related Content
By David Mylet
Was Wm Grant an existing customer?
Yes. We were already supplying between 15%-20% of the site’s cartridge mechanical seals for pumps. The problem was that with over 80% of the seals coming from other suppliers, operators onsite were having to choose from a confusing number of seal face and elastomer combinations. With so many varieties in the store, it was sometimes difficult for the mechanical fitters to select the correct seal for the specific job it had to do. They could be dealing with up to 12 different 35mm dual cartridge seals and a whole variety of seal faces and elastomers.
How did that affect production?
Selecting the wrong seal or a seal with the wrong elastomer meant that there was a very good chance that the seal would fail, which in turn resulted in significant downtime and loss of production. Having to keep so many varieties of seal on site was also inefficient from the point of view of stockholding.
What did AESSEAL® suggest in order to remedy the problem?
We were able to show them how they could simplify the process. We recommended that they should stock one seal type for single seals and one for double cartridge seals. In the end it was quite straightforward. It took only a couple of months working with the store’s team after agreement with the site engineers. The result is that the vast majority of pump cartridge seals are now supplied by AESSEAL®.
Did that mean that they were using just a single elastomer?
This was a key part of the solution. AES-Elast™ is highly versatile and can be used in a wide variety of applications. It’s as close as you can get to a one-size-fits-all elastomer and it’s been particularly successful in the Food and Beverage industry. It’s very resistant to the effects of steam and hot water in the cleaning processes and because it has shown that it can operate in difficult conditions it has a gained a reputation as being very reliable. It’s also FDA-compliant, which is a big selling point in the Food and Beverage sector.
Did it improve seal reliability?
It made a huge difference. The previous MTBF on seals at William Grant was around six months. Our FIDC™ double seals and CURC™ single seals were installed in early 2023. Both types use the AES-Elast™ elastomer, and more than18 months later they’re still working perfectly.
Does AESSEAL offer a follow-up service?
We still carry out regular site visits but with the reduction in seal failures they’re mostly routine. We also work closely with our onsite partners at William Grant’s to manage the stock. Simplifying the process has meant a much higher level of reliability, and standardizing the inventory has resulted in a big reduction in both seal spend and stockholding, with fewer seal types required in the stores.
Is the company satisfied with the results?
Very satisfied. They’ve told us that simplifying the choice of seals along with the use of AES-Elast™ has helped them to achieve a production capacity of 99.4%. They say that removing the risk of fitting the wrong seal has meant a big improvement in reliability and almost zero downtime.