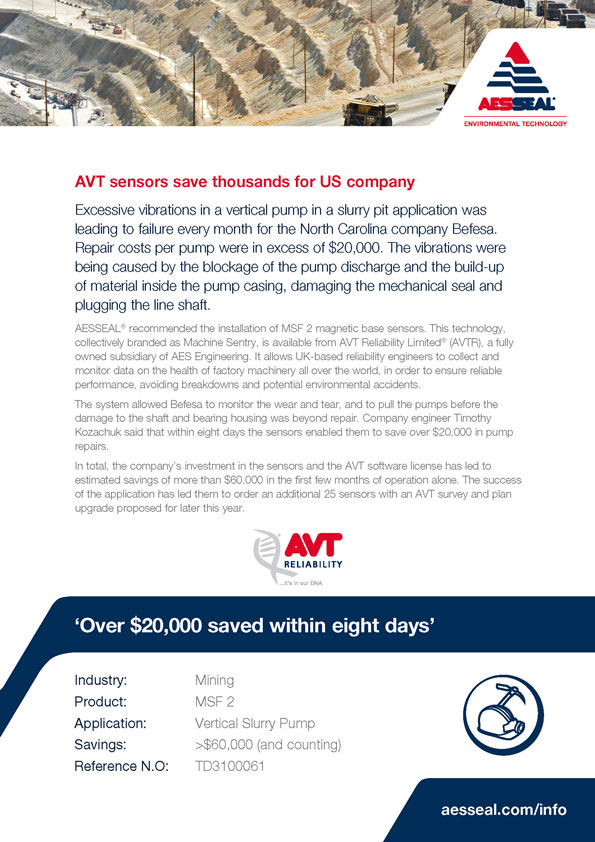
Excessive vibrations in a vertical pump in a slurry pit application was leading to failure every month for the North Carolina company Befesa. Repair costs per pump were in excess of $60,000. The vibrations were being caused by the blockage of the pump discharge and the build-up of material inside the pump casing, damaging the mechanical seal and plugging the line shaft.
AESSEAL recommended the installation of MSF-2 magnetic base sensors
More Industry Related Content
By Dan McCall
Was Befesa an existing customer?
Yes. Befesa specializes in material processing. This includes collecting hazardous waste and residues and recycling them, and processing zinc from raw material and turning it into cast ingots. They were already using our double seals on their slurry pumps. We have also been involved in training and in failure analysis of the seals to help them reduce the overall spend on pump repairs and on the mechanical seals.
What was the nature of the problem?
Befesa uses vertical pumps to pump slurry from a slurry pit. The problem is that the thickness of the slurry can cause the pumps to plug. The blockage of the pump discharge and the build-up of material inside the pump casing causes vibrations, damaging the bearing isolators and shafts.
How often was this happening?
It was happening every few weeks, and the problem was that if it was not detected in time, it could cause severe damage to the pump, which could cost in excess of $20,000 to repair. It was vital to monitor the level of the vibrations so that they could pull the pump before any really serious damage could occur. We set out to show them that the AVT system could do just that.
Were they already aware of the AVT system?
Yes. An engineer at the site had been introduced to AVT while he was working in Canada. When I mentioned that AVT and AESSEAL were part of the same company, he immediately asked for more information about the system.
Did he recommend the system to his managers?
Yes. It took about one month to get the trial moving, but we were able to show them that AVT monitoring would eliminate the need for costly pump repairs and would also reduce downtime. As a result, they agreed to carry out a trial on five sensors. This took place over the course of a few months and was very successful. It convinced them that they could make major savings in repair costs and downtime.
Did this result in further orders?
Yes. They realized that the quality of the vibration data they were receiving from the AVT system meant that they were now able to troubleshoot the cause of any failure and pull the pumps before any major damage could occur. The result was that they installed more sensors and expanded the system to AVT gateways so that they could pull data in real time and send it to the AVT software for monitoring. They now have nearly 50 sensors on site and are working directly with AVT to complete the site survey and set up the pumps so that the sensors can be installed as soon as possible.