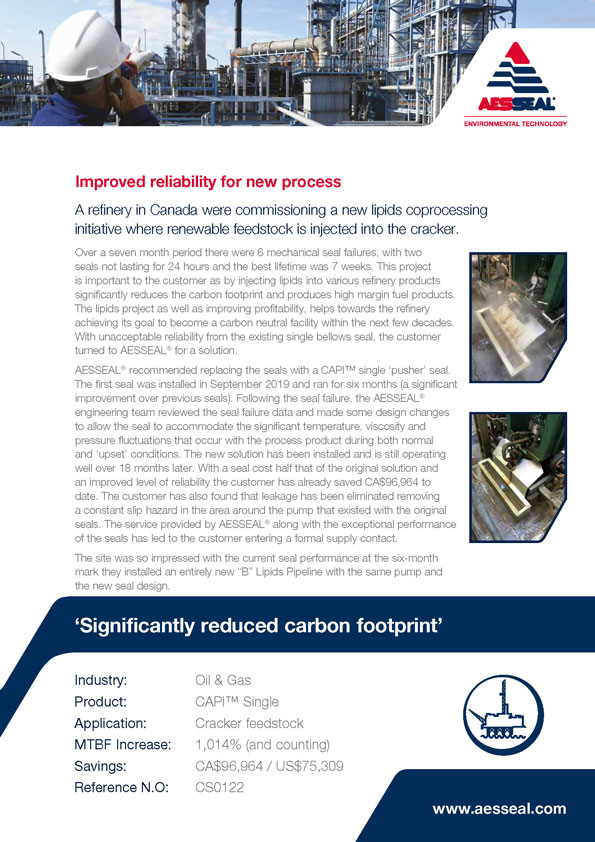
A refinery in Canada were commissioning a new lipids coprocessing initiative where renewable feedstock is injected into the cracker.
More Industry Related Content
By Toby Elston
How did the contract come about?
One of my close contacts from the Pulp & Paper industry was employed at the refinery. He told me that a competitor’s seal on the new lipids co-processing pump kept failing, and each time it was replaced, it wouldn’t last longer than eight weeks.
What suggestions did AESSEAL® come up with?
The competitor seal was a dual-ply metal bellows design. AESSEAL® recommended following the published API 682 4th edition seal selection matrix and proposed a ‘pusher’ type design.
Was it difficult to convince the company to follow AESSEAL’s recommendations?
Not really. We were invited to present our recommendations to the refinery’s senior management team. We explained our seal selection process based on the process application data provided and pointed out the errors in the existing seal design. At the end of the 45-minute presentation, the Maintenance Director instructed his team to purchase our seal. We received the order within a day of providing our first seal quotation.
What were the advantages of the CAPI™ single ‘pusher’ seal?
Metal bellows seals are specifically designed for use in applications where the process temperature is beyond elastomeric limits. They use graphite wedges and gaskets for sealing. Unfortunately, welded bellows are not as robust as pusher seals, and can be susceptible to pressure fluctuations. Pusher seals are far more reliable in design and typically used in as many applications as possible. A pusher seal is always preferred if an application temperature is within an elastomer’s operating range. That’s API 682 4th edition ‘best practices’ recommendation.
From the case study, it appears the CAPI™ seal failed after six months. Why was that?
It was due to the application pipe work. The co-processing pumps were ‘add-ons’ to the site’s existing product transfer pipe network. This pump is subjected to significant high-pressure pulsations, which were intensified to our seal by the plan 11 leg of the API piping plan 14 specified at design. Additionally, the pump was designed without a close-tolerance throat bushing in the seal chamber, so there was no way to control the seal chamber pressure when the pulsations occurred. We had the refinery remove the plan 11 leg of the 14 so it became a 13 (evacuate seal chamber to suction) and modified the seal design to cope with the pulsations. Over three years later, the second seal is still running, and we estimate that in that time it has saved the company around CA$300,000 (US$220,000).
Has the customer given any feedback on seal performance and/or customer service?
Not formally in writing, but the lipids pump was under close scrutiny from the refinery’s senior management team. Our success was noted and gave AESSEAL® the credibility needed to pitch for the full site mechanical seal supply contract. The result was that eight months after this application was completed, the refinery awarded AESSEAL® the preferred mechanical seal supply contract for the entire site. Since then, the refinery has been my primary customer, and I am either onsite or in contact with people onsite on a daily basis.
Has this project led to contracts with other companies which may have learned about AESSEAL® as a result?
Yes, we reference our success with this customer when pitching for new opportunities in the Oil & Gas market. Others in the industry have recognized that success.